The 3D printing technology made headlines in the late 1980s. This was followed by a lull until recently when improvised methods and materials opened up new possibilities.3D printing or additive manufacturing creates a 3D object as per the design fed into a connected computing device. The advantage of utilizing 3D printing is that any object or part, from an industry perspective, can be made from scratch in just hours. It allows designers and developers to create an object from imagination to reality and then ponder about whether or not this prototype will work in the real-life.
Since its inception, 3D printing was mostly utilized in engineering, architecture, and the manufacturing sector. The current scenario has opened up avenues in more sectors, particularly, medical. The technology provides great savings on assembly costs because it can print whole objects. It also allows companies to experiment with new ideas and numerous design iterations without the added expense. This helps in analysing if product concepts are worth to allocate real and additional resources, thus speeding the decision-making process. In the medical industry, it lets surgeons produce artificial body parts for patients who need to be operated upon. Almost everything, ranging from spacecraft components to household objects are being built with the help of 3D printers.
Finding the Perfect Material
To transform ideas into actual 3D models, one needs appropriate material. Few main material types used in 3D printing include plastics ranging from engineering-grade, like PEEK (Polyether Ether Ketone), to easy to use, like PLA. Also, Resin and Composites – combining two materials, and metals are used. All these materials have their own distinctive features and are utilized by industries based on factors like texture, durability, resistance, cost, etc. While the material is usually used in its powdered form, Indmatec, in 2014, became the first company worldwide offering PEEK in filament form. In the following year, it also became the first company worldwide printing PEEK.
HPP155, the first printer dedicated to PEEK 3D-printing, was a product requested by European Space Agency and delivered by Indmatec. By creating the first filament-based additive manufacturing device worldwide, the company started a new way of processing materials that are suitable for medical products and industrial applications. The company soon became famous for its efforts and achievements in the development of High-Performance Polymer Printers. Indmatec continued developing its HPP155 machine until 2016 and eventually, towards the end of the year, the co-founders decided to change the name from Indmatec to Apium Additive Technologies.
Industry Specific Solutions
Apium Additive has always had the vision to create tools where medical products can be manufactured in a resourceful and cost-efficient fashion. It turned out, that additive manufacturing is the ideal process to make that happen. The name Apium refers to the Latin word Apidae which means honey bee. Bees are known to manufacture their structures additively and biocompatible.
The company started freshly in 2017, bringing unstoppable development in the industry with the launch of a new generation printer P155 and also started working on a second, bigger version. It also developed the Apium M220 – a printer dedicated to print PEEK for medical applications. In 2018, the Apium P220 was released, together with a new milestone material- carbon fibre reinforced PEEK with a ratio of 30 % carbon fibres.
Apium could also prove the possibility to print metal green bodies from stainless steel 316L and 17-4PH material, which can be debinded and sintered easily. In 2019, the Apium M220 was launched, fully equipped with an environment inside the printer preventing printing parts from contamination. It also had various safety and quality control features such as an Adaptive Heating System, extensive user management options, an airflow-filter-system, a Door Lock, closed-loop servo motors and camera detection. In the same year, Apium started its own printer production at their facilities and covered a change in management.
Leading with Passion
Apium is led by the three managing directors:
Uwe Popp worked at the University of Stuttgart in cooperation with the Max-Planck Institute of Materials Science and joined the company in 2015 as an engineer.
Dr. Lars Pfotzer studied computer science at the Karlsruhe Institute of Technology (KIT) and earned his doctorate in robotics at the FZI Research Center for Computer Science. He joined as a partner in 2014 and is also one of the co-founders of Apium.
Julian Scholz studied mechanical engineering at the Karlsruhe Institute of Technology (KIT). He joined in 2015 as a development engineer and is a co-founder of Apium.
All three managing directors are fascinated by 3D printing, technology, and materials.
With their diverse backgrounds, they combine different perspectives to a multidimensional management board.
Turning Challenges into Solutions
One of the biggest challenges, anywhere, is to convince potential customers of new technology. Since there is a little experience of a new approach, most of the clients remain hesitant. To counter the challenges, Apium found out that training and case studies are the most successful ways to educate clients as to how additive manufacturing can help them cut down costs and use the new technology properly. The team put in constant efforts to convince design engineers to model parts for 3D printing. They explained how 3D printing gives more freedom and also the different requirements on the design like overhangs, bridging, support, etc.
To be able to process high-performance thermoplastics such as PEEK, Polyvinylidendiflourid (PVDF) or Polypropylene (PP), one needs the right setting of the thermal environment. There are a lot of low-quality FDM printers and materials available, and it was tough to convince clients about the advantage of good quality FFF 3D printing. Apium highlighted the advantage of its printers which lies in the synergy of different disciplines. The team states, “Besides, the knowledge of mechanical and electronic engineering to create a reliable and robust machine, the material science and process knowledge to solidify semicrystalline polymers in their stable solid-state is likewise important.” So far Apium is the only machine manufacturers that can process semi-crystalline parts without needing an additional heat treatment step.
The Focus Area
The applications where Apium’s technology fits best is the medical sector. The team claims that it is possible to print bone replacement parts fitting to each client by having the same manufacturing cost. They add, “The term we are referring to is mass customization, where we can provide an individual implant treatment for an affordable cost. In relation to conventional manufacturing, we could show that a cost reduction to less than a third of the original manufacturing cost is possible.”
Currently the company is focusing on the processing of high-performance materials utilized in the industrial sectors like oil and gas, aerospace, special mechanical engineering. It is also focused on medical applications like printing implants. It is also looking forward to the latest developments in the field like automatic tool changer for using multiple tools like print heads, milling, laser, etc. These developments also leave enough room for more companies to join the industry. The team voices, “There is still plenty of room for a lot of companies providing products and services. So it makes perfect sense to focus on a certain area where those start-ups see their advantage and what they can do best. On the other side is the permanent questioning of concern bearers like, if it had worked out somebody else would have already done it.”
They further advise stating, “In respect to the uprise of this technology, do not give those concerns too much room. There is just not enough time for everybody to do all the things at the same time. There is a reason why those start-ups identified their niche, and this reason will carry them through the struggles they will be facing.”
Discovering Endless Possibilities
Apium Additive is looking forward to the new year with a goal to establish its own additive manufacturing systems as standard tools for the medical production of customer-specific implants. These manufacturing systems are to be used for the production of high-quality components for specific industrial applications. For the team, the next big step is its device becoming a standard tool for medical treatment and providing thousands of patients with affordable medical products.
Additionally, Apium is a part of the first of its kind clinical trial in Europe. The Medizinische Universität Graz is running a clinical study where the whole process from patient CT-scan through slicing, preparing, 3D printing, post-treatment, implantation, and after-care is created, validated and certified for the first time. “This is very unique, since there is no such a certified process for 3D-printed medical parts, yet. With our printer, PEEK-implants will be produced and tested”, the team concludes.
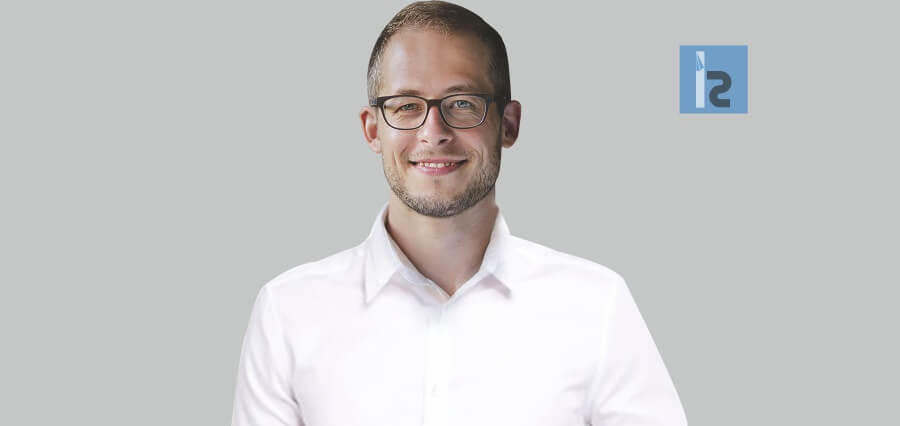
Uwe Popp | Managing Director