In the past few years, almost every manager at every level has discovered some mobile phone application that has proven truly useful to increase productivity.
Perhaps for data gathering, or production status monitoring, or remote communication… there are literally thousands of ways that small devices are changing the ways that we do things… for the better.
And yet…
Have you ever noticed that when you give a child a hammer, suddenly everything needs hammering?
In your own workplace, you have probably (more than once) observed a co-worker trying to use a phone for some purpose that really wasn’t a good fit.
A few examples…
Yamazumi Workload Balancing
A Yamazumi Board is the right tool to rearrange workloads between operators, perhaps for different staffing levels to meet different scenarios of customer demand.
And it is also an excellent tool to visually see and eliminate the 7 deadly types of waste.
Keyword = “see”. Yamazumi is intended to be a group exercise. What is your team going to do? Gather around an iPhone?
Standard Work Analysis
Similarly, a phone might be useful for time observation, process observation, muda waste walk observation… but process analysis?
The purpose of gathering all of that observation data is that (at some point) someone needs to Analyze and Improve the process.
A Standard Work Analysis Excel template performs 7 simultaneous types of analyses, to answer common (and important) questions like: “How long will this take?” “How much does this cost?” “How many can we make?” “How many could we make if we did a SMED quick changeover kaizen event with the goal to reduce setup times by a target amount?” “What should be the target for that kaizen event?”
Try answering THOSE questions using only your Samsung.
Value Stream Mapping
The primary purpose of a value stream map is to make process flow visible.
The title of the book that introduced value stream mapping is Learning to See. Learning to see process flow. Learning to see process wastes. Learning to see opportunities for how to do things better. There’s that word again: “See”.
How is your team going to ‘see’ the overall flow of your entire process on a 3-inch screen?
That’s not enough screen space for even the top third of a value stream map, that has all those symbols that show the flow of the information needed to control the flow of ‘the thing being processed’, (which might be a product, or a patient, or a packet of information).
The bottom third has charts and graphs to make some of the most important data more visual (and actionable). Charts showing total lead time split into segments for value add time vs. wait time. Showing how costs accumulate through the steps of the process. Showing the cycle times for each step in relation to your target takt time.
And the middle third has rows and rows of data (each row optionally hidden or revealed), to answer mission-critical questions like: “Can capacity meet demand?” “Where is our bottleneck?” “What is our Guaranteed Turnaround Time?” (the longest that it will ever take to delivery any product or service in this family)
Mystery Solved
Why is Microsoft Excel still so popular?
Those are just a few examples to explain why Excel is still so popular. (Visit the systems2win.com web site for a hundred more.)
Especially when extended with the power of add-ins, Excel does things well that a phone simply isn’t designed to do.
About the Author
Dean Ziegler is the founder of Systems2win (systems2win.com). They develop and support an Excel add-in with 150+ templates for Continuous Process Improvement, each with training, videos, and systems for popular lean methodologies like process flow optimization, standardized work, visual management, FMEA risk reduction, quality improvement, OEE preventive maintenance, and lean management systems.
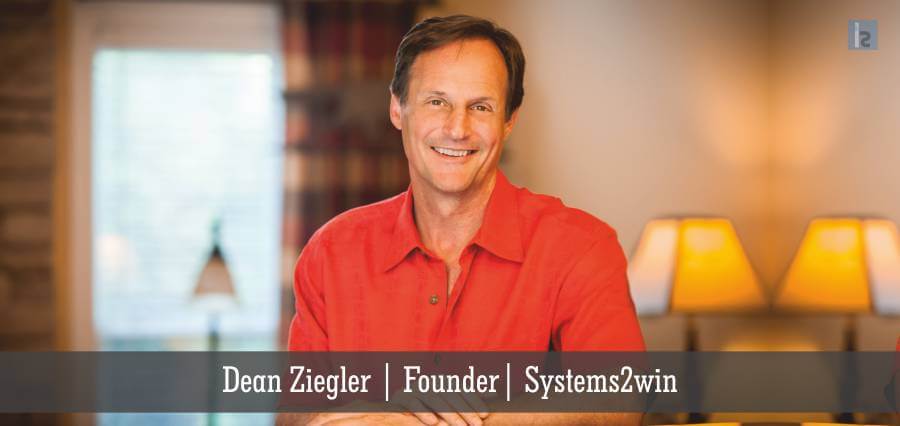